ニュース
パナソニック コネクトの機内エンタメ機器の現場へ! 日本で“モノ作り”をする、そのこだわり
Astrovaの製造・検査の現場に息づく、日本品質のモノ作り
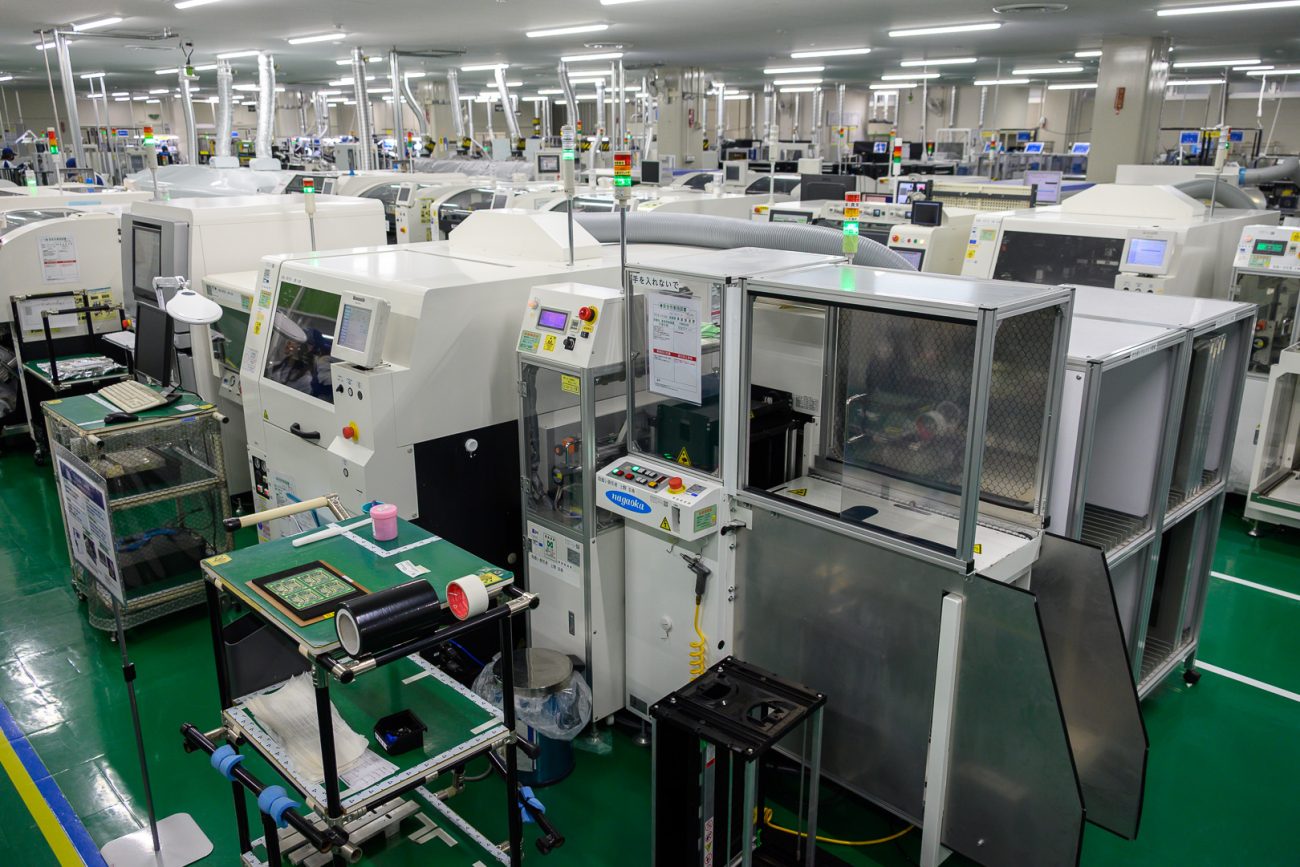
では、北門真で行なわれている、このAstrovaの製造現場を紹介しよう。今回は、製造、そして検査・検証の工程を中心に見学した。
製造は、まずSMT(表面実装技術)と呼ばれる工程で、システムの基板を作り上げ、それをOLEDパネルと接着後、筐体へ組み込んで製品が完成する流れとなる。
SMTは基板へのはんだのプリント、各部品の取り付け、基板にはんだ付けするリフローと、自動的に進められていく。このSMTの自動化システムもパナソニック製だ。繰り返しになるが、20年や30年といった長期サポートを求められるのが航空業界の特徴である。長期サポートをするにはその企業が存続し、事業が持続しているのが前提となるだけに、こうした製造機械もグループ内で調達できるというのは事業の持続性の観点で意味あることだろう。
ちなみにSMT工程の最後には、防水加工のためのコーティングが施される。突然の揺れでドリンクが飛び散って、それが原因で電気がショート、火災発生…といったことを起こさないためだ。その後の基板とOLEDの接着では、高い精度が求められるために、接着面をプラズマ洗浄したうえで接着剤を塗布するという。
そして、筐体への組み付けは人の手で行なわれている。しかし、各作業台はカメラで記録しており、その映像をセンシングしてデータ化。製造上の課題解決や、計画的な生産へと活かしている。
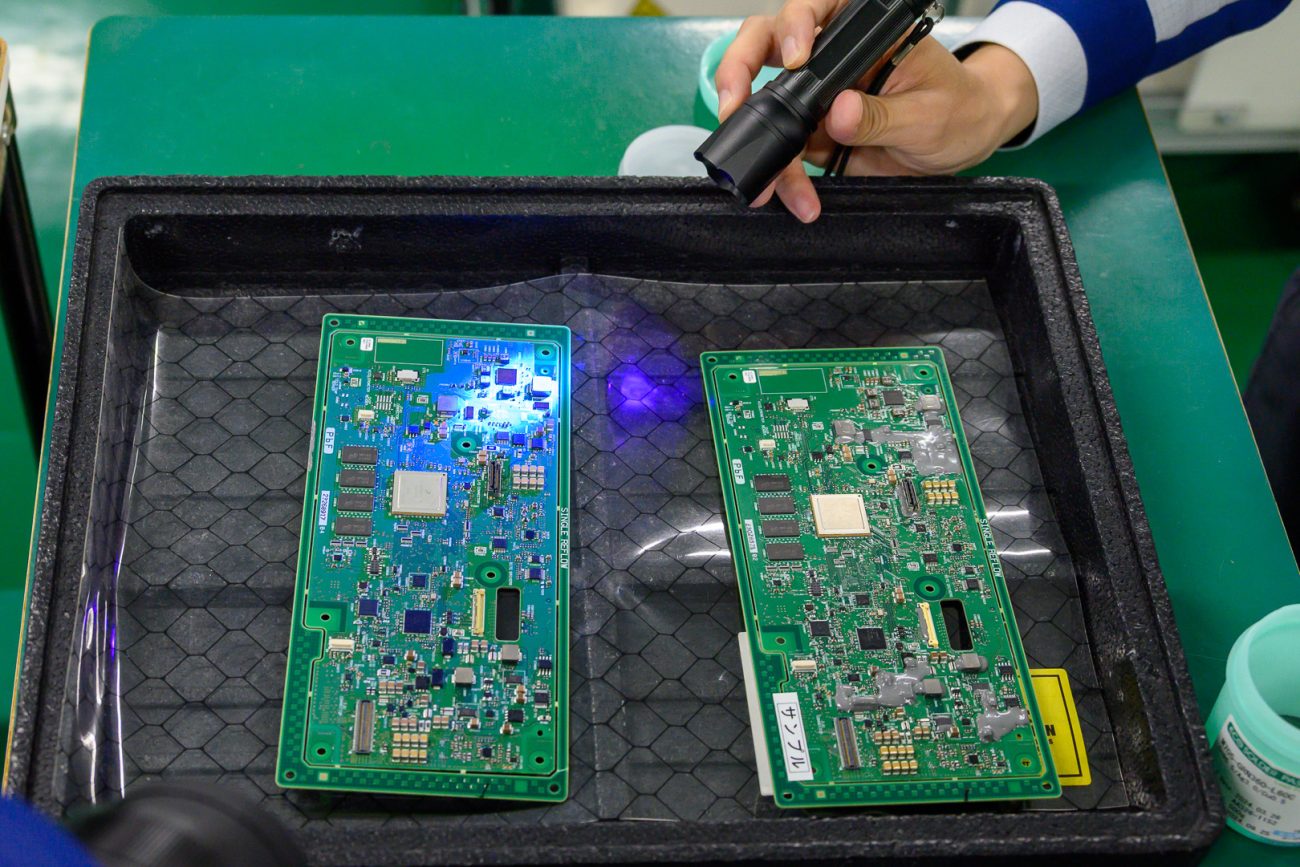
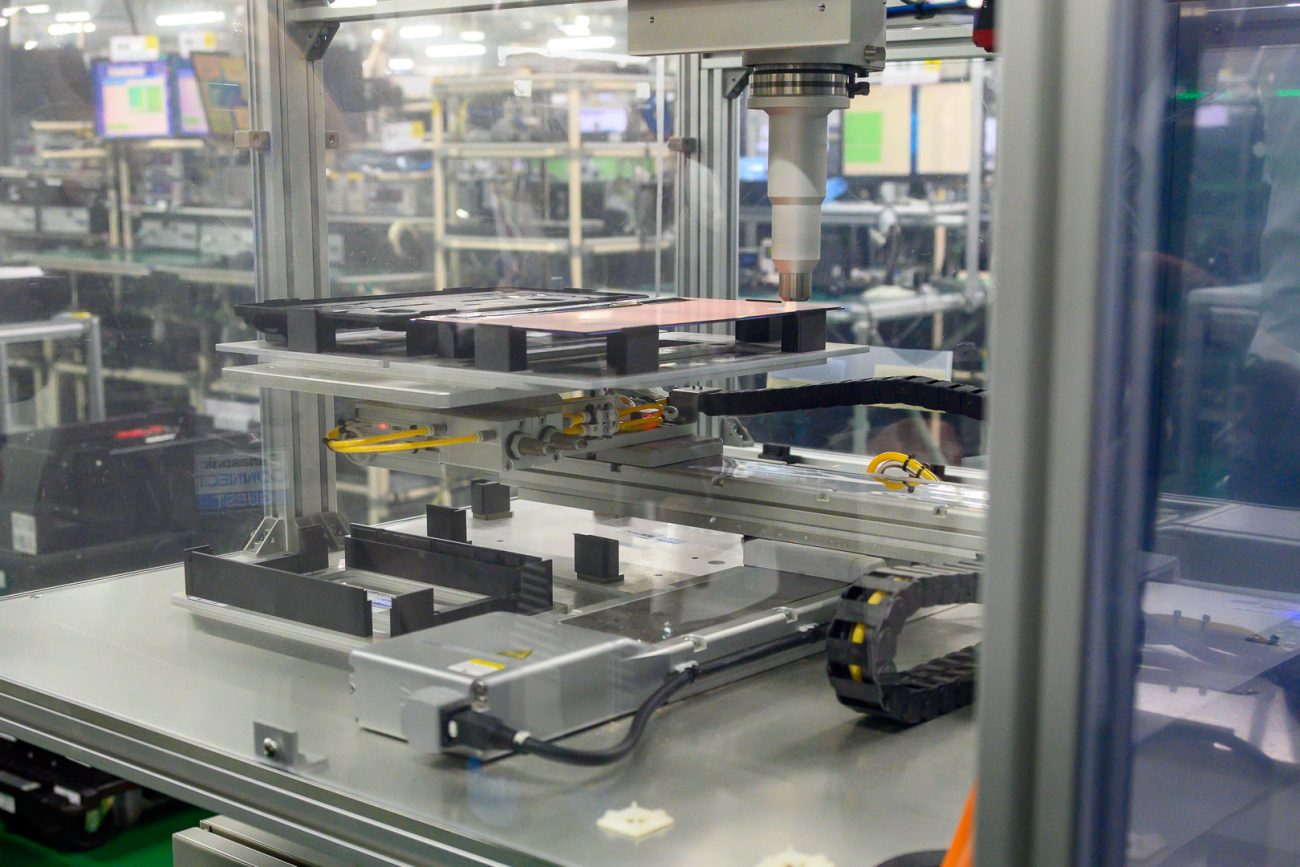
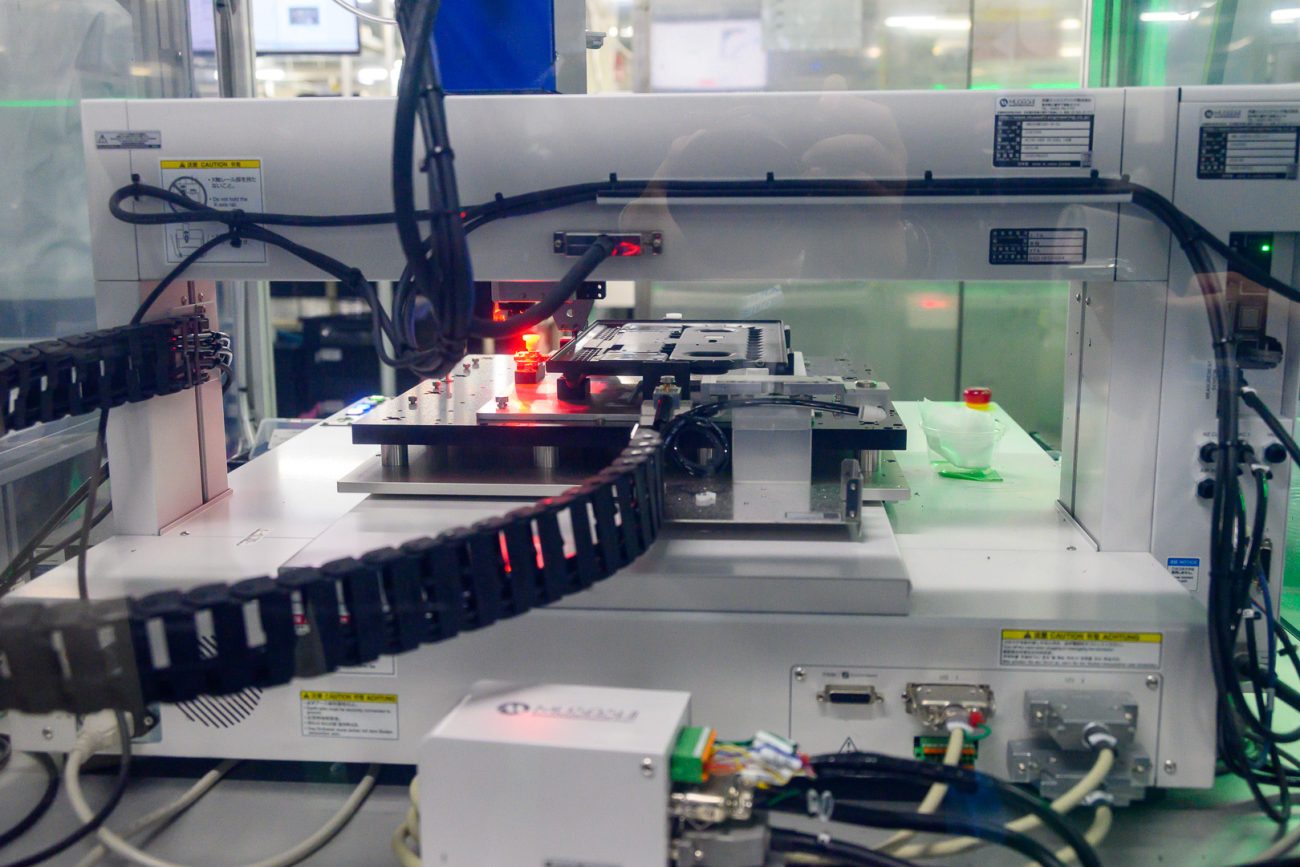
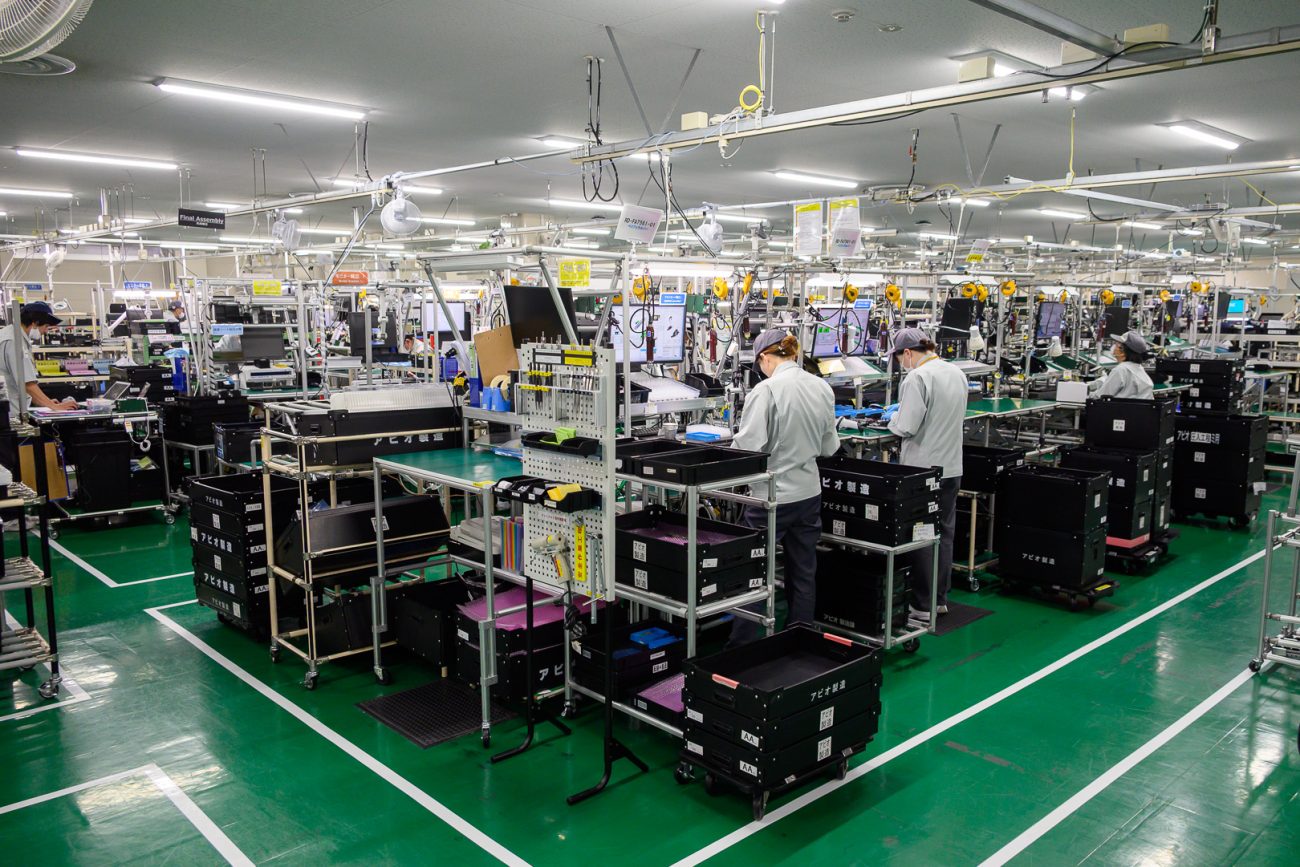
製品の検査・検証の工程は、大きくハードウェアの検査とソフトウェアの検査に分かれる。ソフトウェア面の検査室は多数のモニターが並んでおり、飛行中の動作を想定したテストを行なっている。また、スクリプトに沿ってモニターをタッチできる小型のロボットも導入しており、タッチ操作が正常に行なわれるかも検証している。
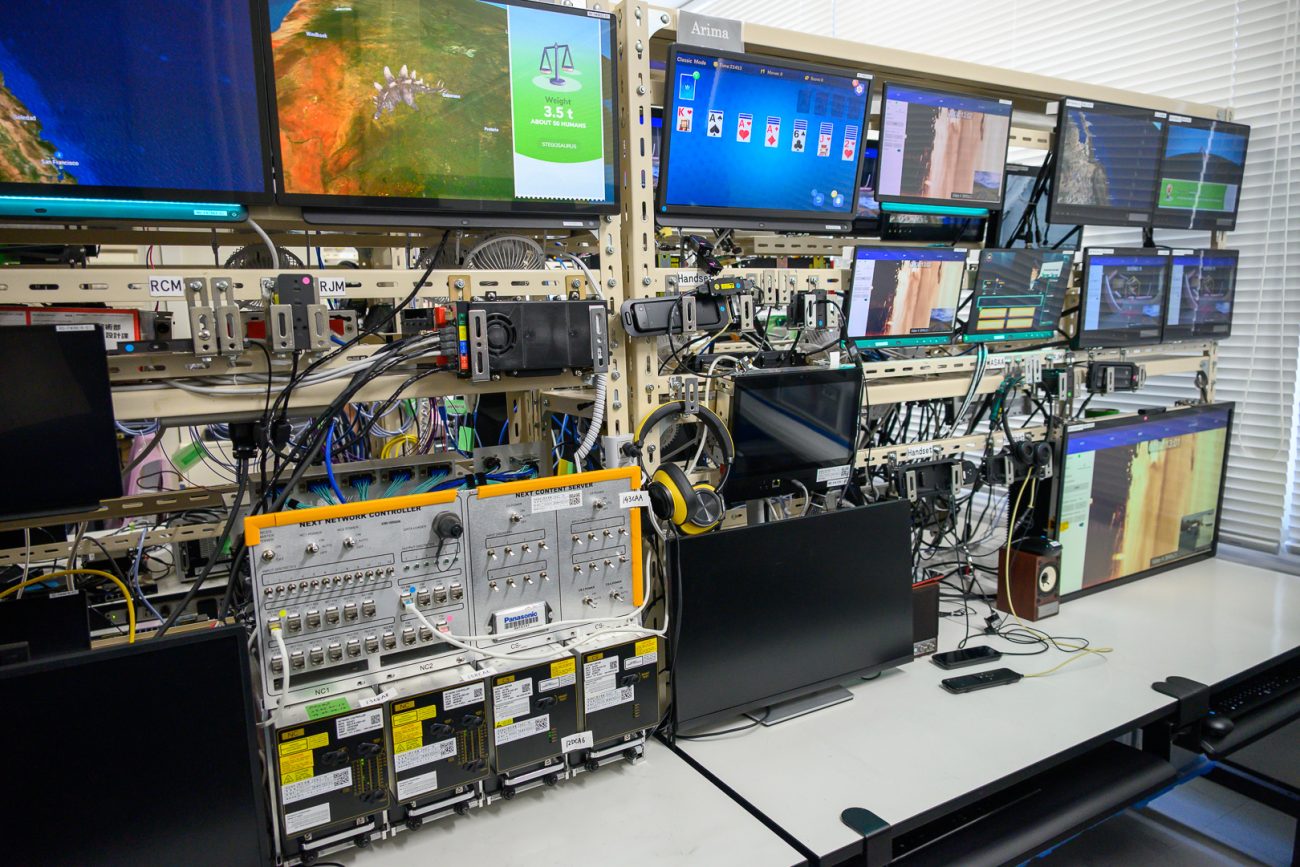
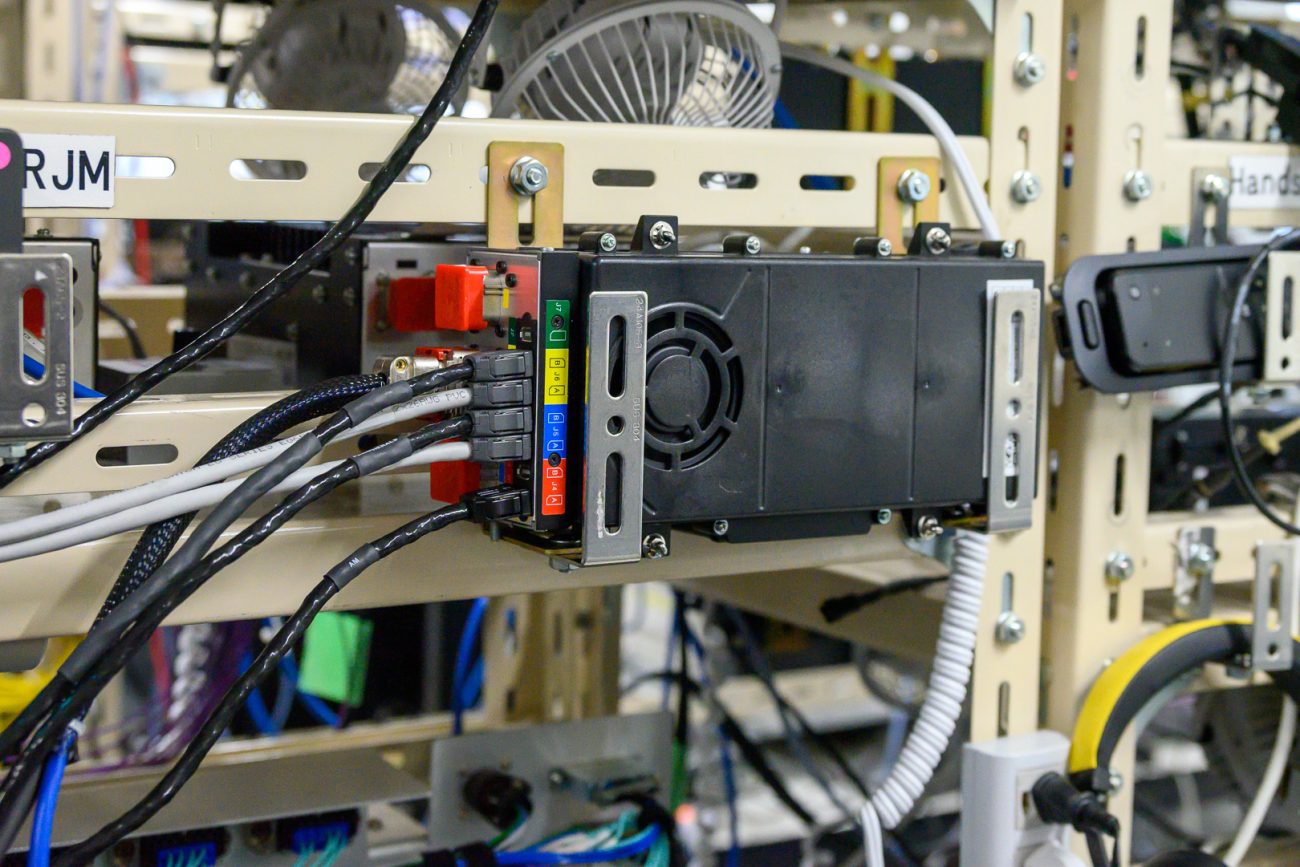
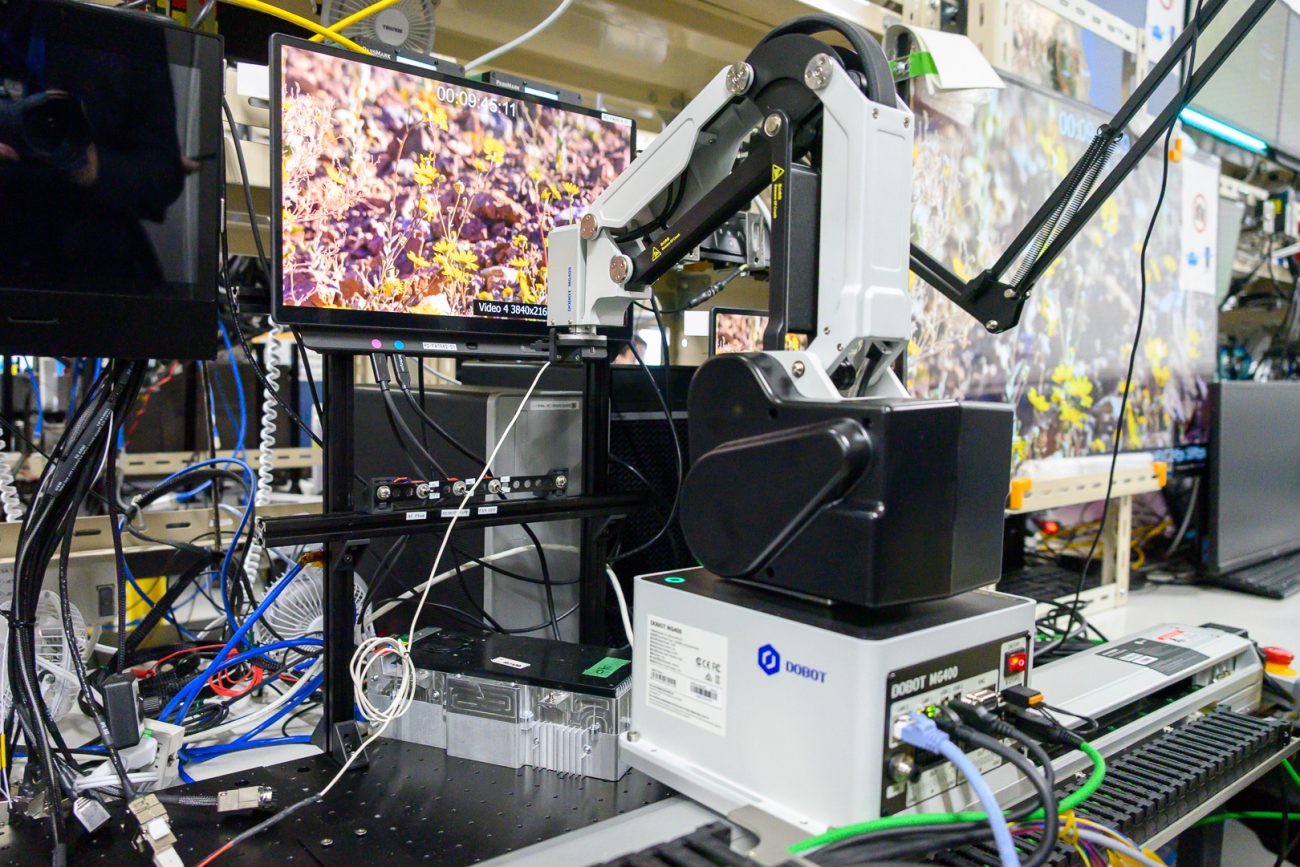
ハードウェアは、主に過酷な環境への耐性を検証するものとなる。またしても繰り返すが20年、30年といった長期的なサポートが必要となる機器だけに、いわゆる“加速試験”と呼ばれる、温度、湿度ともに通常よりも過酷な環境に製品を動作させ、長期的な動作の変化、物理的な劣化などを確認する手法が採られる。
実際に見学した検査では、サウナのような容器や部屋のなかで検証が行なわれ、なかには高温かつ振動を加えるという検証もあった。もちろん、逆に超低温での検査や、急激な温度変化など、さまざまなシナリオに沿って検証が行なわれている。
こうした検証を繰り返すことで重要なのは、端的に表現すると“壊れ方が分かる”ことだ。劣化しやすい部位や故障直前の予兆などを把握できることは、製造段階での品質向上につながるだけでなく、すでに航空機に搭載している機器の予防保全などにも役立つ情報となるのである。

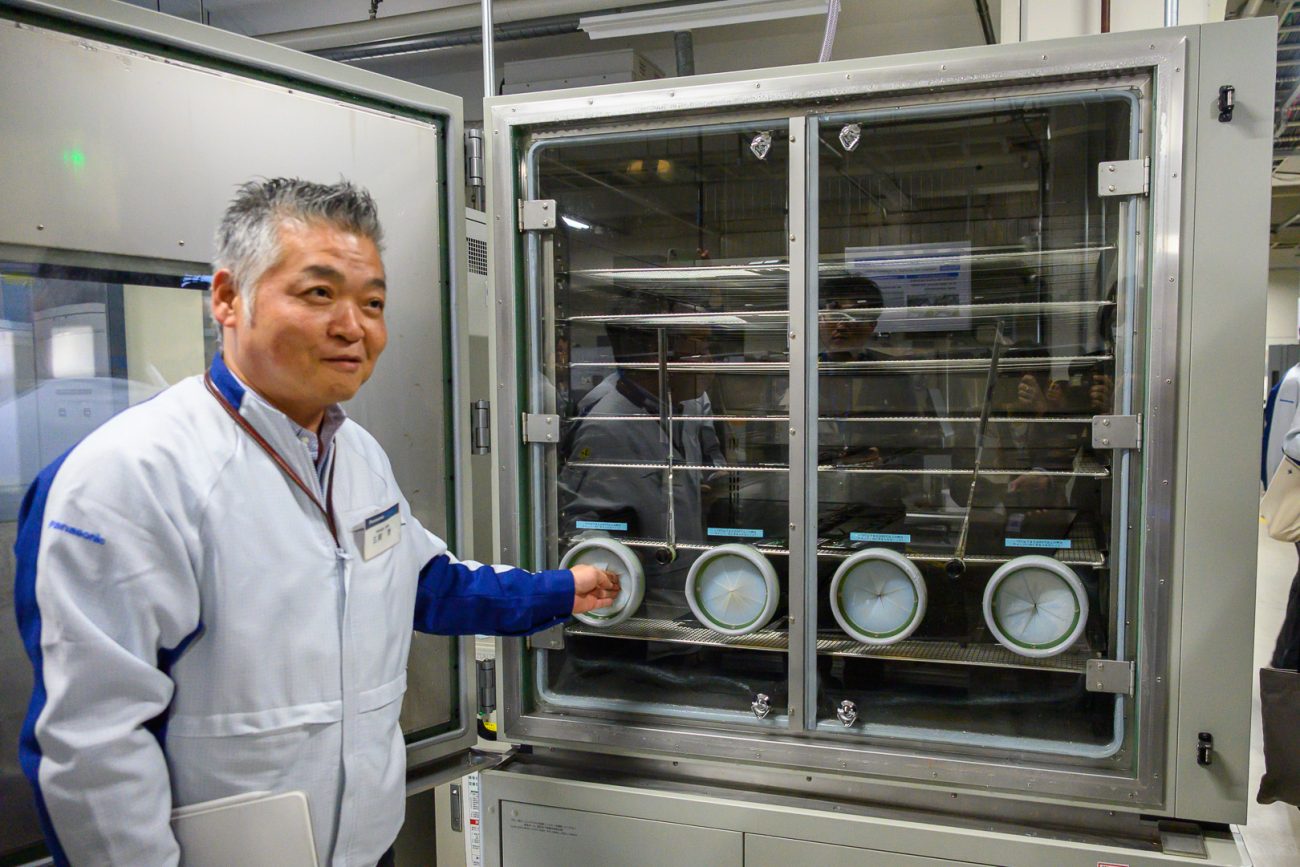
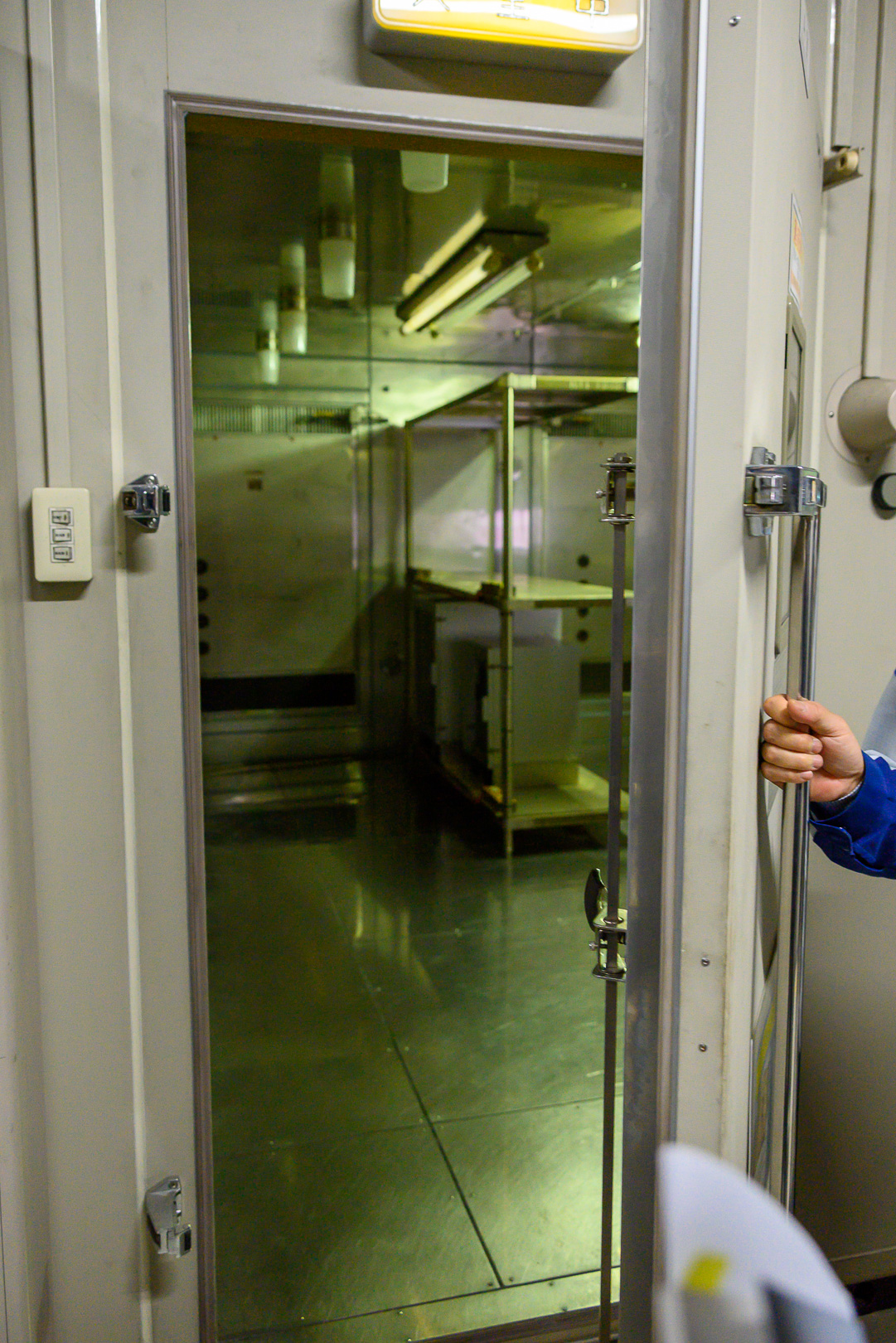
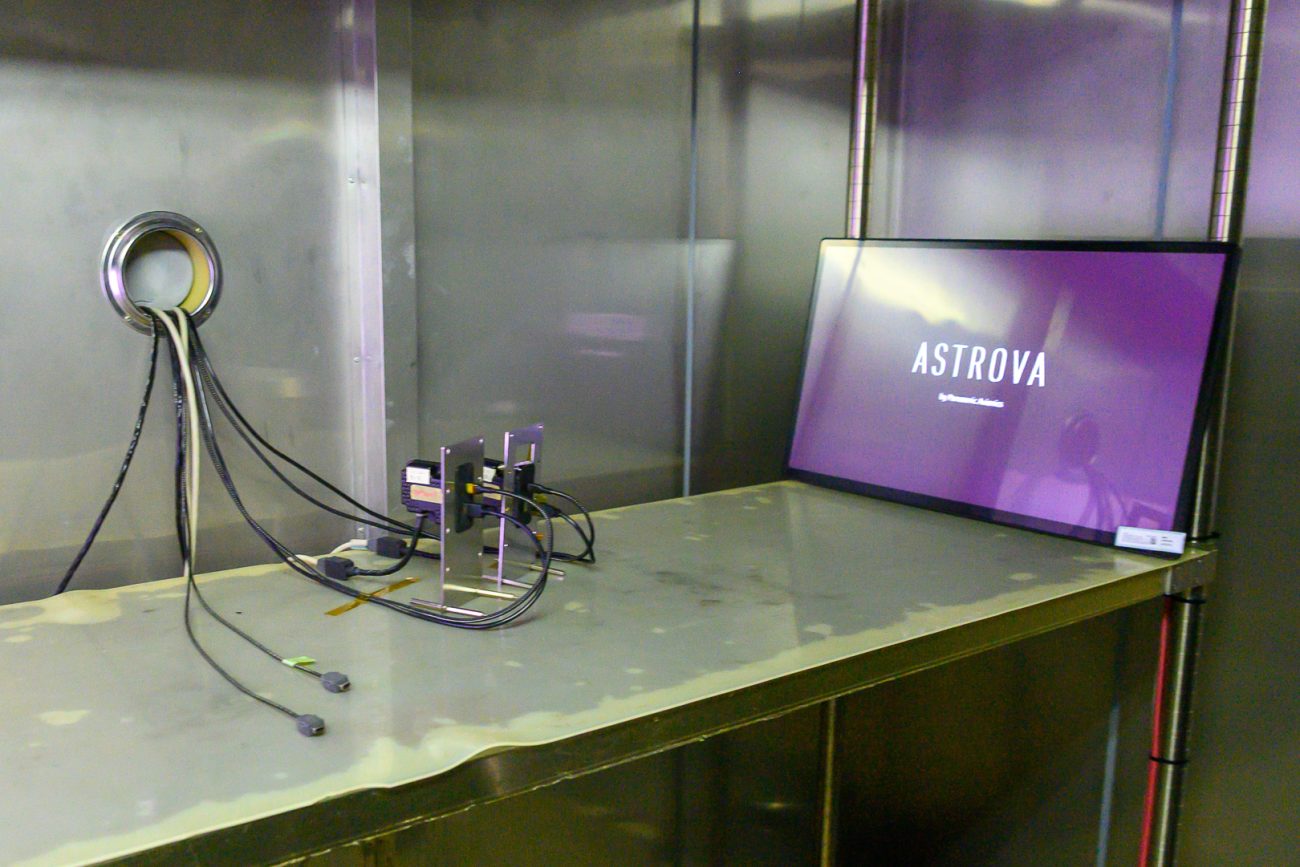
言うまでもなく、厳しい試験を繰り返すのは高い品質=航空業界が求める品質の製品を提供するためである。航空機に搭載する機器は、すべて米連邦航空宇宙局(FAA)や欧州航空安全機関(EASA)といった当局の承認(耐空証明)が必要で、その承認を前提に航空機メーカーが各機種への搭載可否を認定することになる。
パナソニック コネクトのアビオニクス事業には、FAA認定検査員が複数名在籍しており、自社で必要な検査を実施することができる。北門真で製造し、北門真で必要な検査を完結させ、そのまま航空機メーカーや航空会社へ納入できる体制が作られている。
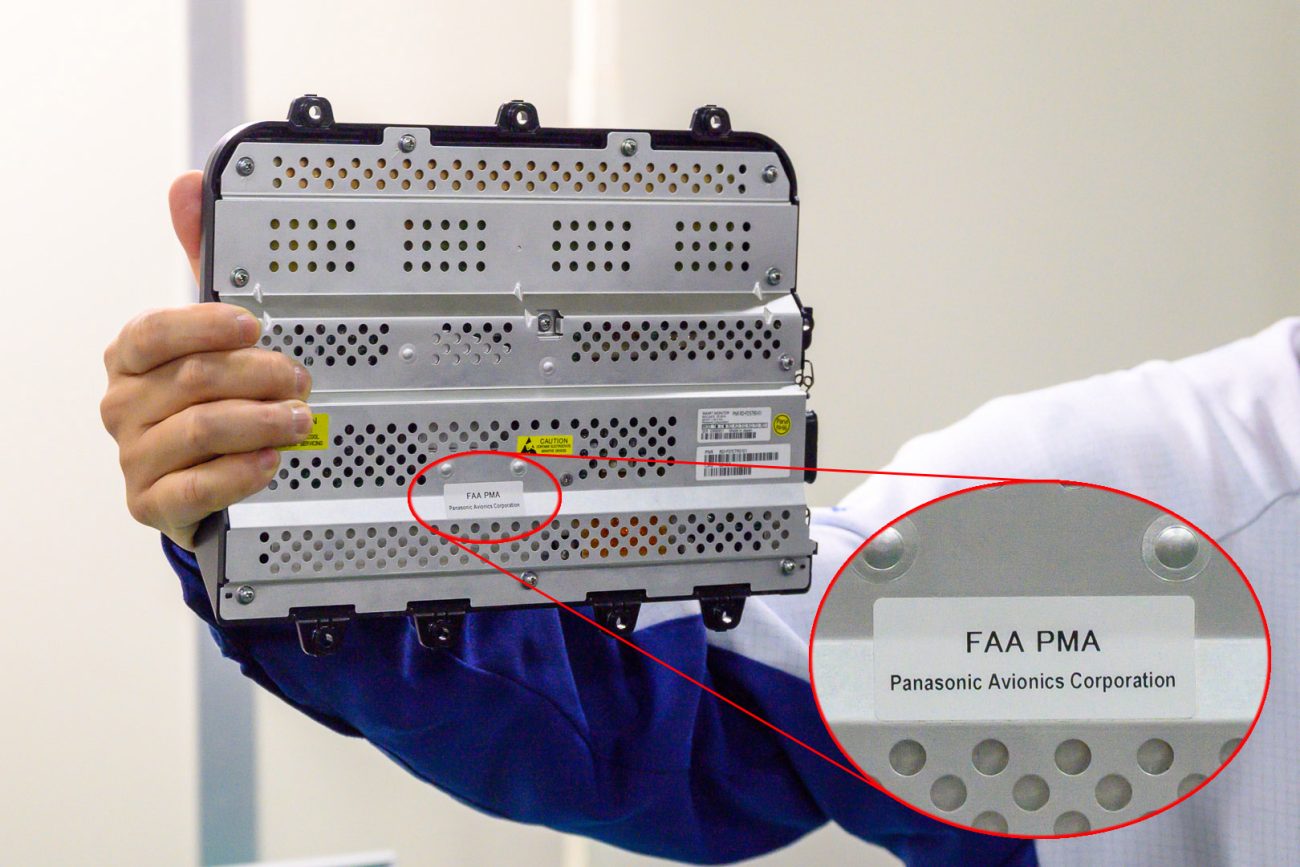
パナソニック コネクトの次の一手は?
さて、ここまでパナソニック コネクトの最新製品とその製造現場をお伝えしたが、この先にはどのような展開を考えているのだろうか。
まず、製造をすべて日本で行なっている同社にとって、日本の生産年齢人口が減少していくリスクには備えなくてはならない。加藤氏は「データでサプライチェーンやエンジニアリングチェーンをつなぐ、データドリブンな製造拠点を、日本で実現したい」と述べ、品質の維持、モノ作り力の強化といった土台を大前提に、業務の変革に取り組んでいく考えだ。
加えてAIについても言及があり、長年のアビオニクス事業で蓄積したデータとAIを活用することで、顧客サポートに役立てているという。また、周辺環境に応じた映像の調整や、言語の壁を越えた客室乗務員とのコミュニケーションに活かすといったビジョンも示された。
他方、パナソニックブランドの航空ソリューションのもう一つの柱として、機内インターネット接続のシステムがあるが、こちらも現在新たなシステムが開発途上だ。
高軌道の静止衛星(GEO)による既存のインターネット接続に加え、低軌道の衛星(LEO)にも対応したマルチ・オービットなアンテナの開発を進めている。このアンテナはデジタル的に指向性を変えるビームフォーミングに対応しており、従来のものより薄型化も実現。
ちなみに、LEOはStarlinkに代表される低軌道衛星に接続することで、衛星を介したインターネットとして、より高速(低遅延)にアクセスできるものとなる。パナソニック コネクトのアンテナはOneWebが展開する衛星コンステレーションと接続する。
まさに、2025年4月3日に、セスナ・サイテーションを利用した飛行中の接続試験も行なわれ、LEO接続で最大193Mbpsという高速なアクセスを達成したという(Panasonic Avionicsのニュースリリース)。
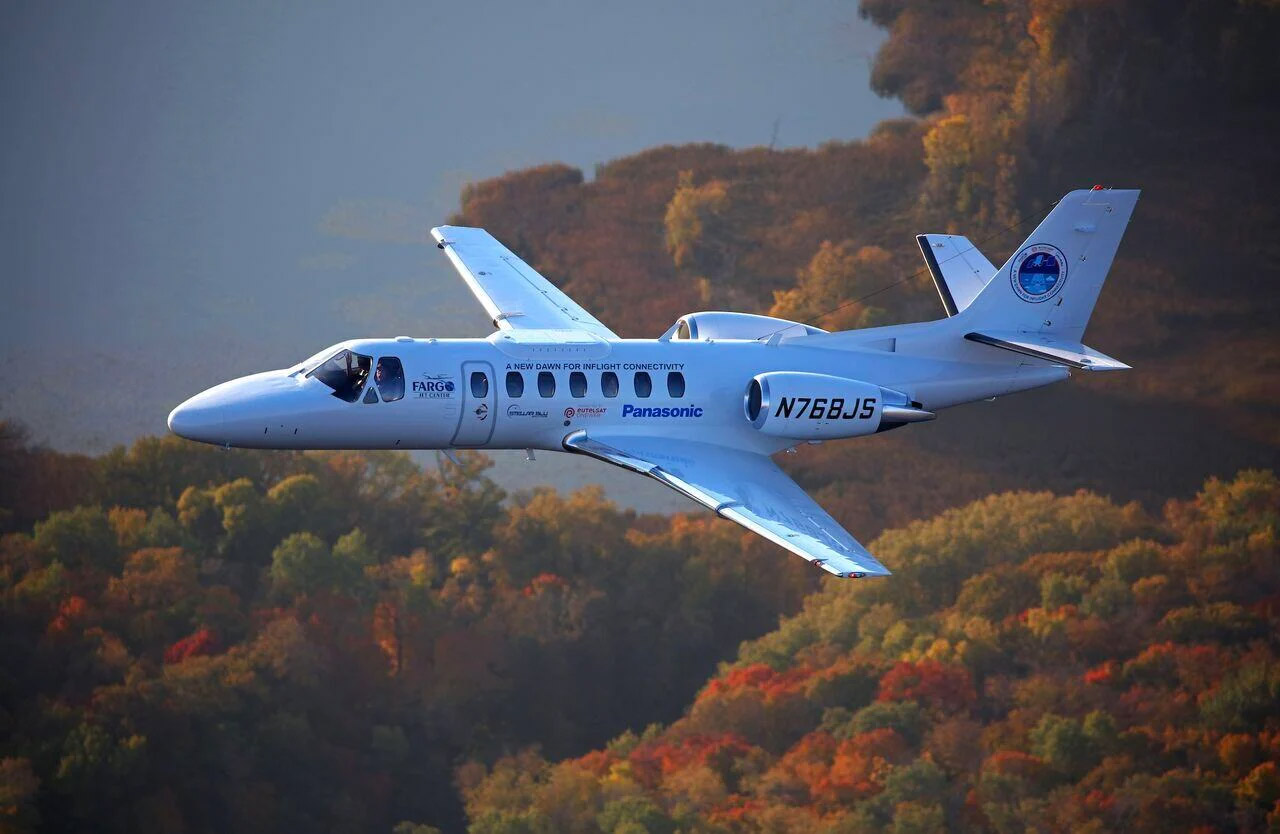
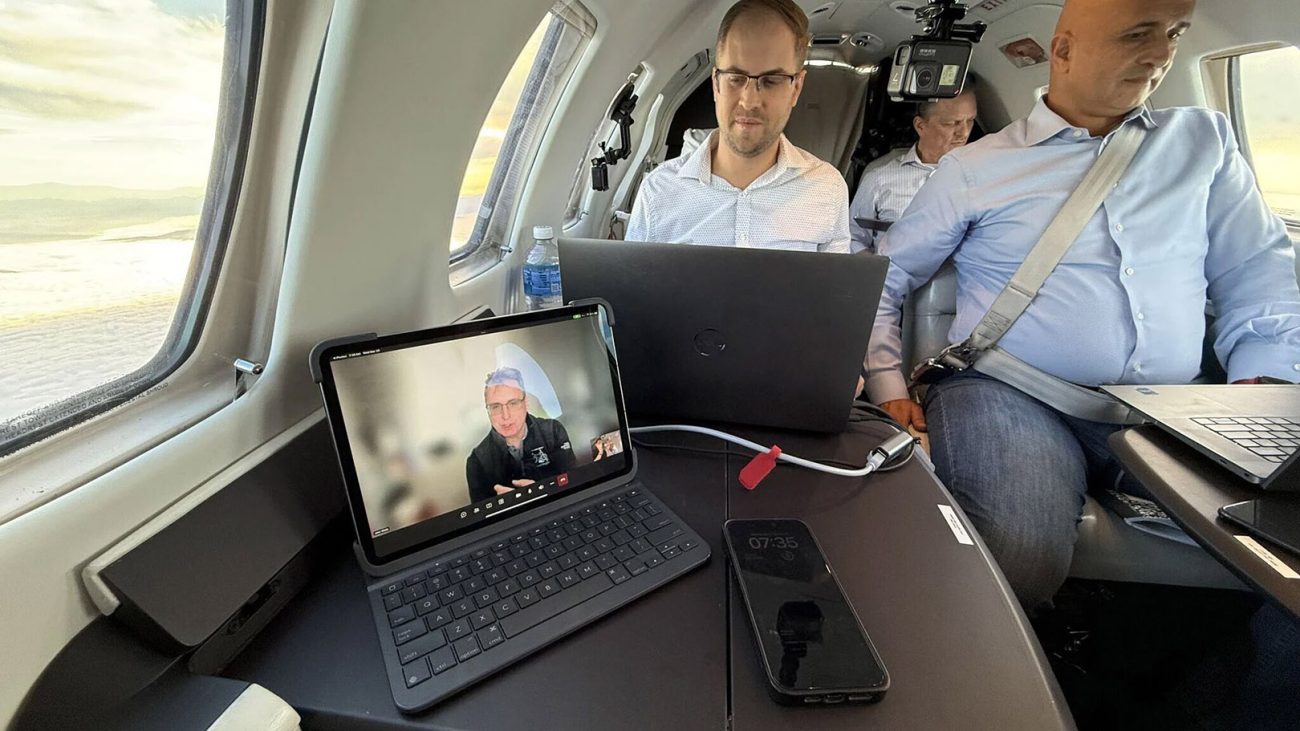
このように、まだまだ新たな製品の開発を進めるパナソニック コネクト。日本製の高品質を前提に、乗客である私たちの機内体験が今後どのように向上していくのか。楽しみは尽きない。
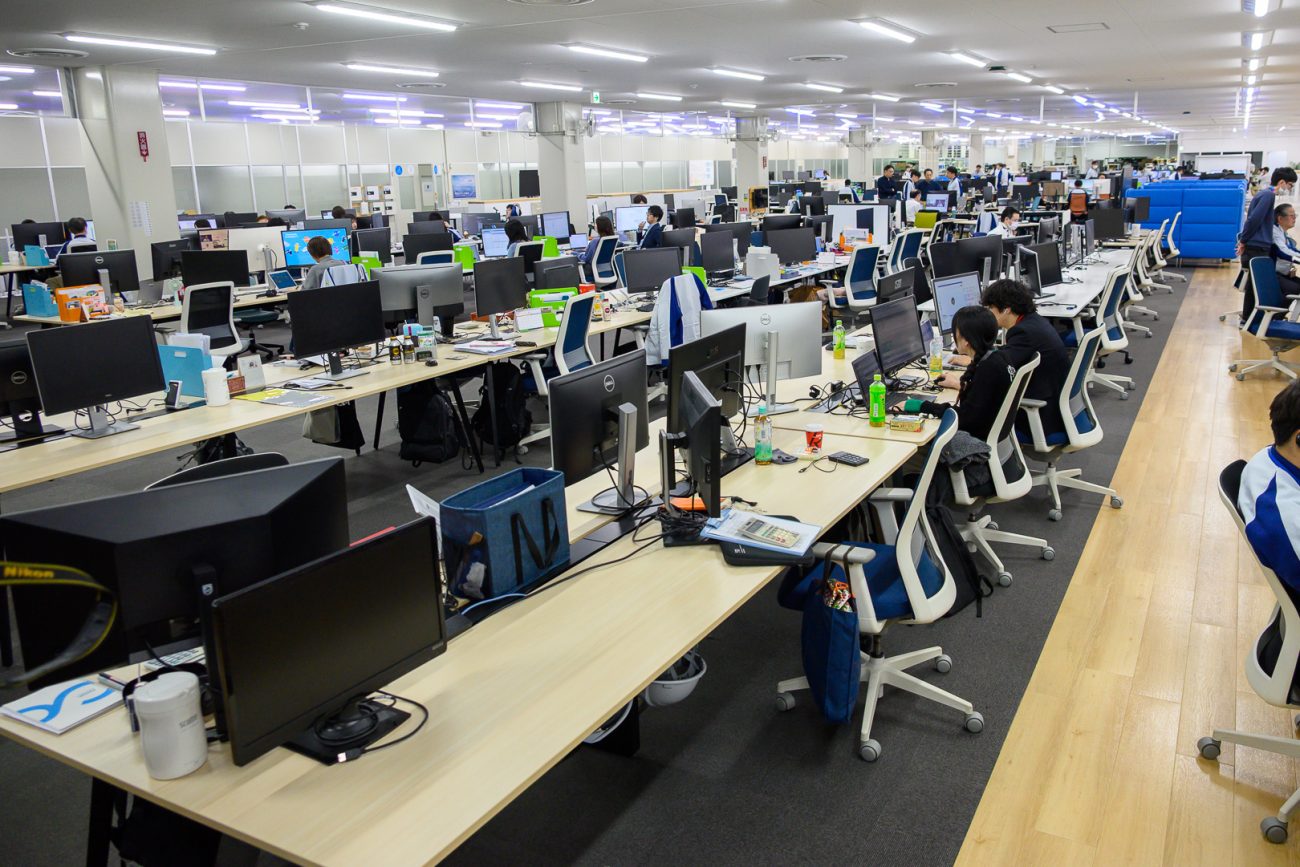
関連記事
関連キーワードもチェック!
関連リンク